Die Herstellung von geschmiedetem Edelstahl ist ein mehrstufiger Prozess: Stahlschrott wird geschmolzen und dann in eine bearbeitbare feste Form gegossen; der erstarrte Stahl wird geformt, wärmebehandelt, gereinigt und poliert, um die gewünschten Spezifikationen zu erfüllen. Schließlich wird der fertige Edelstahl verpackt und an die Hersteller versandt.
Schmelzen und Gießen
Stahl und Legierungsmetalle werden in einen Lichtbogenofen geladen. Im Ofen wird das Metall auf eine bestimmte Temperatur über seinem Schmelzpunkt erhitzt, normalerweise über 2800 °F. Aufgrund der extremen Temperaturen, der Präzision und der großen Mengen, die für die Stahlproduktion erforderlich sind, dauert der Schmelzvorgang im Allgemeinen 8 bis 12 Stunden. Während dieser Phase überprüfen Stahltechniker regelmäßig die Badtemperatur und die chemische Zusammensetzung. Nachdem die Stahllegierung vollständig geschmolzen ist, wird die Mischung raffiniert. Argongas und Sauerstoff werden in den Ofen gepumpt, wo sie einige Verunreinigungen in Gas umwandeln und andere dazu bringen, Schlacke zu bilden, die leicht entfernt werden kann. Der raffinierte Stahl wird in maschinenfertige Formen gegossen, darunter Blöcke (Rechtecke), Knüppel (rund oder quadratisch), Brammen, Stangen und Rundrohre.
Bildung
Das Warmwalzen erfolgt oberhalb der Rekristallisationstemperatur des Stahls. Der meiste Gussstahl wird durch Warmwalzen hergestellt: Die Bramme, der Block oder der Knüppel wird erhitzt und durch riesige Walzen geführt, wodurch der Stahl in eine längere, dünnere Form gestreckt wird. Jede Bramme wird zu einem Blech, einer Platte oder einem Streifen geformt, während Blöcke und Knüppel zu Drähten und Stangen geformt werden. Kaltwalzen wird verwendet, wenn präzisere Abmessungen oder ein besserer Oberflächenglanz erforderlich sind. Es erfolgt unterhalb der Rekristallisationstemperatur des Stahls. Beim Kaltwalzen werden Räder mit kleinem Durchmesser und einer Reihe von Stützrädern verwendet, um glatte, breite Bleche aus rostfreiem Stahl mit engen Toleranzen herzustellen.
Wärmebehandlung
Durch Wärmebehandlung wird gewalzter Edelstahl durch Rekristallisation der verformten Mikrostruktur gestärkt. Die meisten Edelstahlsorten werden durch Glühen wärmebehandelt – der Edelstahl wird auf eine Temperatur genau über seiner Kristallisationstemperatur erhitzt und unter kontrollierten Bedingungen langsam abgekühlt. Dieser Prozess löst innere Spannungen und macht den Edelstahl weicher. Glühtemperatur, -dauer und -abkühlungsgeschwindigkeit wirken sich alle auf die Eigenschaften des gesamten Stahls aus.
Entkalken
Ein gewalztes Stück Edelstahl weist eine Schicht oxidierten „Zunders“ auf, die abgewaschen werden muss, um eine glänzende Oberfläche wiederherzustellen. Zunder wird normalerweise durch chemische Mittel wie Elektroreinigung und Beizen entfernt. Beim Beizen wird der Edelstahl in ein Bad aus Salpeter-Flusssäure getaucht. Bei der Elektroreinigung werden eine Kathode und Phosphorsäure verwendet, um Strom an die Edelstahloberfläche zu leiten. Beide Verfahren entzundern die Oberfläche effektiv. Das entzunderte Metall wird abschließend mit einer Hochdruckwasserspülung gereinigt, wodurch eine helle, glänzende Oberfläche entsteht.
Schneiden
Edelstahl wird auf eine bestimmte Form und Größe zugeschnitten. Der Großteil des Zuschneidens erfolgt mechanisch – der Edelstahl kann mit Kreismessern geschert, mit Hochgeschwindigkeitsklingen gesägt oder mit Stanzen gestanzt werden. Manchmal werden auch alternative Methoden wie Flammen-, Plasma- und Wasserstrahlschneiden verwendet.
Fertigstellung
Edelstahl kann mit einer Vielzahl von Oberflächenveredelungen hergestellt werden. Die gewählte Oberflächenveredelung ist nicht nur ästhetisch – bestimmte Veredelungen machen Edelstahl korrosionsbeständiger, leichter zu reinigen oder einfacher in der Fertigung zu verwenden. Die Art der Veredelung wird durch die beabsichtigte Anwendung bestimmt. Oberflächenveredelungen sind das kombinierte Ergebnis von Herstellungsprozessen und Veredelungsmethode. Warmwalzen, Glühen und Entzundern erzeugen eine matte Oberfläche. Warmwalzen, gefolgt von Kaltwalzen auf Polierwalzen, erzeugt eine glänzende Oberfläche, während eine Kombination aus Kaltwalzen, Glühen und Polieren mit einer feinen Oberfläche eine reflektierende Oberfläche erzeugt. Bei der Veredelung von Edelstahloberflächen wird eine Reihe von Schleif-, Polier-, Schwabbel- und Sandstrahlgeräten verwendet.
Kaltverfestigung
Kaltverfestigung ist der Prozess der Materialverfestigung durch Verformung. Rostfreie Stähle härten insgesamt schnell aus, wobei die genaue Geschwindigkeit von der jeweiligen Güte abhängt. Austenitische Stähle härten leichter aus als andere Güten.
Qualitätskontrolle und Inspektion
Während der gesamten Herstellung und Verarbeitung von rostfreiem Stahl gibt es prozessbegleitende Kontrollen, aber das reicht nicht aus, um internationale Qualitätsstandards zu erfüllen. Vor dem Versand muss jede Charge rostfreien Stahls chemischen und mechanischen Tests unterzogen werden, um sicherzustellen, dass sie die gewünschten Spezifikationen erfüllt. Mechanische Tests messen die physikalische Fähigkeit eines rostfreien Stahls, Belastungen, Spannungen und Stößen standzuhalten. Mechanische Tests umfassen die oben in den mechanischen Eigenschaften beschriebenen Zugfestigkeits-, Brinell- und Zähigkeitstests. Chemische Tests überprüfen die genaue Chemie einer Probe, bevor die rostfreie Stahlsorte zertifiziert wird. Chemische Tests werden normalerweise durch zerstörungsfreie spektrochemische Analyse durchgeführt. Die Korrosionsbeständigkeit ist bei rostfreiem Stahl von besonderer Bedeutung. Stahlwerke testen und messen die Korrosionsbeständigkeit mit Salzsprühtests – je länger der Stahl nach der Einwirkung von Salzsprühnebel korrosionsfrei bleibt, desto höher ist die Korrosionsbeständigkeit.
Herstellung
Edelstahl ist ein äußerst nützliches Material, das zur Herstellung einer großen Produktpalette verwendet wird. Der Großteil des Edelstahls wird an einen Hersteller geliefert, wo er weiter geformt, wärmebehandelt, bearbeitet und geschweißt wird, um ein bestimmtes Produkt herzustellen. Edelstahl wird häufig zur Herstellung von Komponenten für die Automobil-, Schiffs-, Flugzeug- und Lebensmittelindustrie verwendet, um nur einige zu nennen.
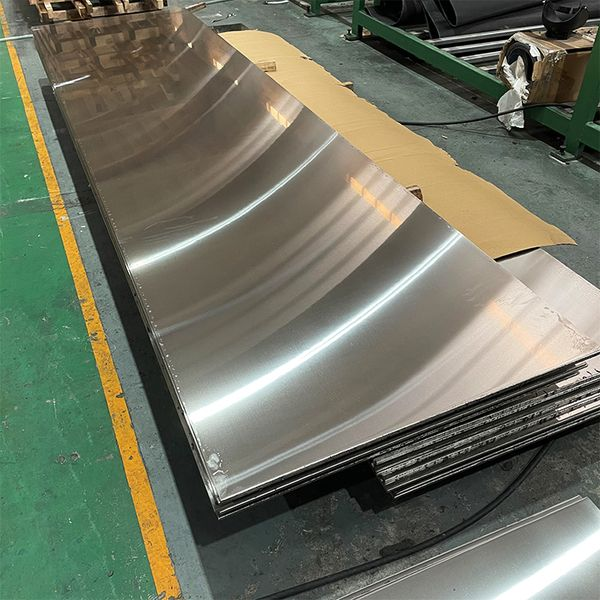