DFM, conception pour la fabricabilité, fait référence à la prise en compte des capacités de fabrication pendant le processus de conception du produit. Un rapport DFM permet d'identifier en amont les problèmes de conception, d'apparence, de fonctionnalité et de fabrication, ce qui permet une évaluation et une amélioration. Cela permet de réduire le temps et les ressources consacrés au prototypage répété, d'économiser les coûts de main-d'œuvre et de matériaux, d'améliorer la qualité de production du produit et d'accélérer le processus de fabrication. Il intègre les spécifications de conception, les exigences de fabrication, les capacités de processus et la gestion de projet, le tout visant à minimiser les problèmes de production.
En fonction du procédé de fabrication, la conception pour la fabrication peut être adaptée à des procédés tels que le moulage par injection, l'emboutissage, le moulage sous pression et diverses autres méthodes d'usinage. Cet article se concentre sur l'usinage à titre d'exemple.
La qualité d'un rapport DFM reflète directement l'expertise et les compétences des ingénieurs de processus, ce qui a un impact sur la qualité du produit et les coûts de fabrication. En fin de compte, il met en valeur la compétence globale d'une entreprise.
Pour créer un rapport DFM, le personnel concerné doit maîtriser les logiciels de CAO, de capture d'écran et de bureautique (généralement PowerPoint). Le logiciel de CAO est un outil de dessin professionnel, nécessitant au moins des compétences de base. Pour les structures de produits plus complexes, un logiciel de dessin 3D peut être utilisé pour faciliter les explications dans la présentation. Le logiciel de capture d'écran est relativement simple et peut être utilisé à l'aide d'outils tels que WeChat ou QQ pour capturer des images. Les compétences en logiciels de bureautique sont également de base.
Voici un aperçu du contenu généralement inclus dans un rapport DFM de base :
Informations de base sur le produit
Cette section consiste principalement à renseigner les informations relatives au produit du client. Elle comprend les détails suivants, qui doivent être renseignés conformément aux données et aux dessins fournis par le client :
Ce rapport se concentre principalement sur les informations relatives au développement de produits, y compris les métaux. matériel, dessin numéro, version, exigences techniques, poids, etc. Ces détails sont de la plus haute importance et nécessitent une confirmation supplémentaire avec le client, en particulier dans le cas d'exigences techniques et de spécifications matérielles, où toute erreur doit être absolument évitée. La plupart de ces informations sont généralement obtenues à partir des dessins fournis par le client.
Processus de fabrication du produit
Cette section sert de bref aperçu du processus de fabrication du produitLa pièce est constituée d'une surface cylindrique, de filetages et d'un trou central, avec des exigences strictes en matière de précision et de rugosité de surface sur deux dimensions critiques. L'étiquetage des dimensions sur le dessin est complet et les profils de dimension sont clairement définis. Le matériau utilisé est le S45C. Ci-dessous, nous recommandons d'inclure un dessin de produit en 2D pour faciliter la compréhension du processus de fabrication.
Ci-dessous, nous vous présentons une introduction basée sur le processus de production, depuis l'arrivée de la matière première (matériau scié) à l'usine jusqu'à l'emballage final et la livraison du produit fini. Après le processus de fabrication décrit, l'ébauche de matière première passe par les étapes de tournage (AB), de meulage, de nettoyage et d'emballage avant de devenir le produit fini.
Lors de la création d'un rapport DFM, il est essentiel de respecter le processus de fabrication et de prendre en compte des aspects tels que équipement d'usinage, équipement d'inspection, outillage, emplacements d'usinage, nettoyage, et conditionnementLes exigences de processus pour la pièce concernent principalement les dimensions structurelles, la plage de traitement et les exigences de précision. Le choix de la précision de contrôle de l'équipement est déterminé en fonction des exigences de précision, qui englobent la précision dimensionnelle, la précision de positionnement et la rugosité de surface de la pièce.

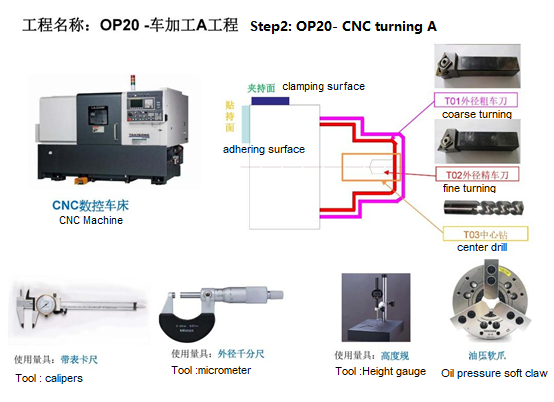
Déterminez les exigences de processus pour les composants, la taille du lot pour l'usinage des pièces, décrivez les caractéristiques requises pour le tour CNC et faites une sélection raisonnable de tour CNC pour répondre aux exigences de processus des composants.
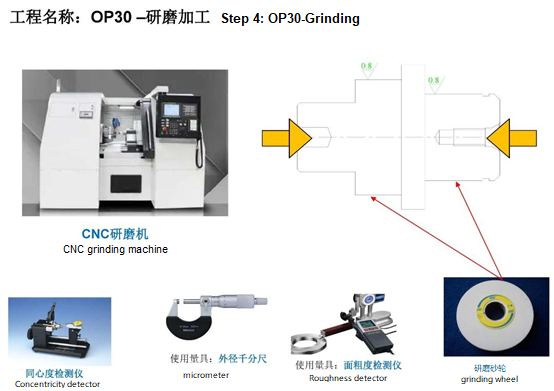
Exigence d'impression de code
Les exigences d'impression des produits sont décrites ici. Ces détails doivent être confirmés par le client. Le contenu de l'impression est soit fourni par le client, soit décidé par le biais d'une discussion mutuelle. Les exemples courants incluent l'impression de numéros de série et de codes QR.
L'inspection finale est effectuée sur les produits une fois tous les processus de production terminés et avant leur mise en stock. Les types courants d'inspection finale comprennent l'inspection complète, l'inspection visuelle du produit fini, GP12 et d'autres.
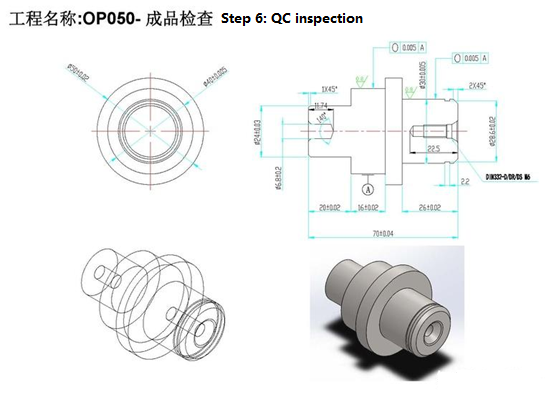
La détermination du poste de nettoyage dans la ligne de production a un impact significatif sur la propreté du produit. Ce produit répond aux exigences de nettoyage standard. En ce qui concerne l'emballage, il est généralement nécessaire de soumettre une proposition d'emballage à l'approbation du client
analyse du problème
Lors de la préparation du briefing, il est essentiel de soulever rapidement avec le client les problèmes liés aux dimensions du produit et aux aspects techniques. Ces problèmes peuvent inclure l'indisponibilité de matériaux spécifiques et la possibilité d'utiliser des matériaux alternatifs, ainsi que des préoccupations concernant le respect des exigences dimensionnelles sur les dessins, entre autres. En plus d'identifier ces problèmes dans le briefing (clairement signalés), il est également essentiel de proposer des modifications raisonnables aux dimensions du produit et aux exigences techniques.
Les avantages de la mise en œuvre de la conception pour la fabricabilité (DFM)
Qualité et fiabilité améliorées : en prenant en compte les processus et les contraintes de fabrication dès la phase de conception, DFM contribue à améliorer la qualité et la fiabilité globales du produit.
Manufacturabilité et testabilité améliorées : DFM garantit que les produits sont conçus de manière à maximiser la facilité de fabrication et de test, réduisant ainsi la probabilité de problèmes de production et de test.
Délai de production réduit : les pratiques DFM rationalisent le processus de conception et de fabrication, contribuant ainsi à mettre les produits sur le marché plus rapidement et à réduire le délai de production.
Coûts de production réduits : en optimisant les conceptions pour faciliter la fabrication et l'assemblage, la technologie DFM peut conduire à des économies de coûts importantes pendant la production, par exemple en réduisant le besoin de processus de fabrication complexes et chronophages.
En faisant du DFM un élément central du processus de développement de produits, ces avantages peuvent être réalisés, conduisant à un développement et une fabrication de produits plus efficaces et plus rentables.
Résumé
Dans les processus de développement de produits traditionnels, il existe souvent un décalage entre la conception du produit et les processus de fabrication. Ce décalage peut entraîner une mauvaise fabricabilité, des difficultés d'assemblage, des modifications de conception importantes, des cycles de développement de produits longs, des coûts de production élevés et des difficultés à garantir la qualité du produit, empêchant parfois la production de masse.
Grâce à l'application des principes de conception pour la fabricabilité (DFM), nous pouvons résoudre les problèmes liés au choix des matériaux, au choix des processus et à l'analyse des coûts des composants. Le DFM est une approche efficace de développement de produits qui permet de réduire les coûts de fabrication, de raccourcir les cycles de développement de produits et d'améliorer l'efficacité globale de l'entreprise.
Une fois le rapport DFM terminé, l'étape suivante consiste à entamer des discussions avec le client. Ce n'est qu'une fois que tous les détails de fabrication ont été confirmés avec le client que le projet peut être transmis au chef de projet pour le développement de nouveaux produits.
Les idées présentées ici sont basées sur l'expérience pratique de l'auteur en matière de recherche et de production allégée. Il est important de noter que l'applicabilité de ces principes peut varier en fonction de l'environnement de travail et de l'expérience spécifiques, et qu'ils peuvent ne pas couvrir tous les scénarios possibles.
Bien entendu, une fois le rapport DFM terminé, l'étape suivante consiste à entamer des discussions avec le client. Il est essentiel de confirmer tous les détails de fabrication avec le client avant de transmettre le projet au chef de projet pour le développement du nouveau produit.
Les idées partagées ici sont basées sur l'expérience pratique de l'auteur en matière de recherche et de production allégée. Il est important de reconnaître que l'applicabilité de ces principes peut varier en fonction de l'environnement de travail et de l'expérience spécifiques, et qu'ils peuvent ne pas couvrir tous les scénarios possibles de manière exhaustive..